
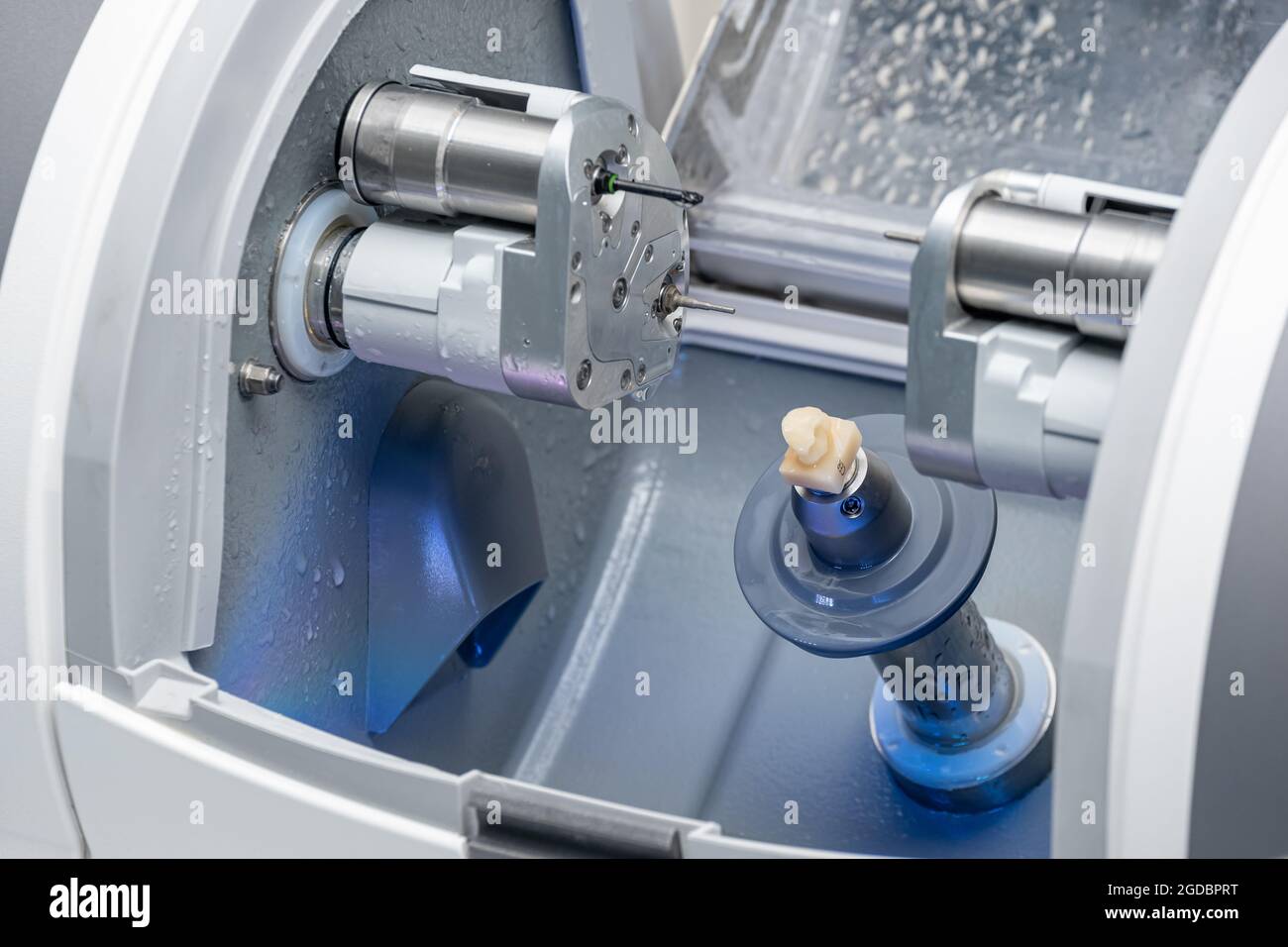
Most mills are configured to operate as either a wet or dry mill.
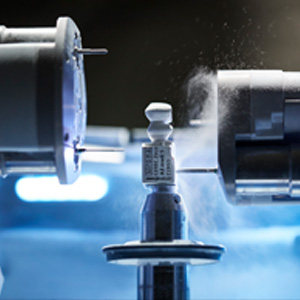
Vacuum size, noise, and operating expense should all be considered before making a purchase. Maintenance cleaning is still required, as a considerable amount of dust and shavings are generated with dry milling. Wet mills require periodic cleaning because the material milled away collects within the machine and eventually needs to be removed.ĭry milling does not use liquid to remove scrap material from the cutting surface, but rather pressurized air, vacuum, or a combination of both. Certain additives can also be included in the liquid to act as a cutting lubricant. It continuously bathes the cutting tool and milling stock, keeping both the tool and material cool, and helps to remove material from the milling disk or block. The liquid in a wet mill serves several functions. In general, wax and acrylic (for temporaries) are milled dry. Other materials, such as zirconia and titanium, can be milled dry or wet. Certain ceramic materials such as lithium disilicate and feldspathic porcelains require wet milling, as do some metals like chrome cobalt. The type of material being milled determines whether a mill should be dry or wet. The milling program generated by CAM software tells the controller inside the milling machine how fast the spindle should spin. It consists of an encapsulated motor inside the mill that spins the cutting tool (bur). The spindle is the heart of any milling machine. From dry or wet milling to chairside or laboratory mills, the options appear to be endless. Patients enjoy the instant results and clinicians can perform more procedures in office.īuying a dental milling machine is a big – and often confusing – decision. Since mills are located chairside (in office), clinicians can place restorations in a single office visit. Dental milling machines take the digital impression and design a clinician has created to mill restorations in the same day.
